
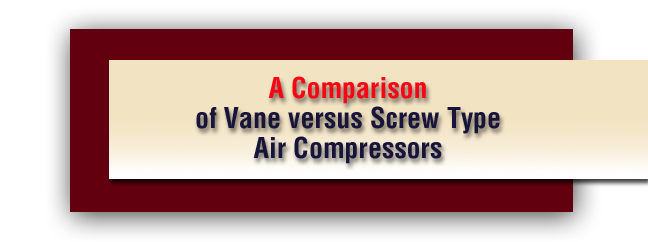

|
A
screw compressor is most efficient when it is new. The clearances
are minimum, leakage is minimum and MEP (mean effective pressure)
is minimum. As the compressor wears the clearances enlarge. Leakage
of air to intake and to preceding pressure cells increase, which raises
the MEP. The effect is to reduce the air delivery and increase the
H.P. required to compress the reduced quantity of air.
The vane compressor will not degrade with wear but will actually improve.
As the blades seat in on the stator and rotor slots, leakage and power
are reduced and the compressor stabilizes at a level 5 to 10% higher
efficiency than when new. This level is maintained by the clearances
being maintained at minimum throughout the life of the compressor
wear.
The rotors of the screw compressor are made of steel of a very easy
machinable grade. This is because of the large amount of metal removal
and numerous machining operations. This type of steel is prone to
galling under marginal lubrication conditions. A pair of rotors that
have been in service for less than 2000 hours will have gaps in the
sealing lands on the O.D.s of the lobes, and numerous scars
on the flanks of the lobes. As a result of metal to metal contact
during each and every start up, galling occurs that is the result
of the welding that takes place between similar malleable metals without
lubrication. The surface of the metal is not porous and does not retain
oil for start up.
The vane compressor has the rotor, stator and end covers of high quality
cast irons. Cast iron is a superb bearing material because of the
free carbon, hard iron carbides and porous surface which retains oil.
There is no contact between these parts, only between them and the
blades. If the blade is made of a material that is dissimilar and
wear resistant then galling is eliminated and wear is reduced. The
Davey Permavane blade is made of such a material and processed to
produce a highly wear resistant blade. |

|
It
is impossible to produce lobe forms, which mesh perfectly throughout
the cycle. During most of the cycle leakage paths exist, which allow
air to escape from the H.P. zone to the intake. The leakage through
these paths is constant regardless of speed, and the displacement
of the compressor is a function of speed. The effect of this is that
the percentage of leakage lessens at higher speed and increases at
lower speed. This low speed characteristic will cause the screw compressor
to absorb high H.P. at low rotational speeds. Because the vane compressor
does not have these paths the torque demand of the compressor will
decrease as the speed lowers. |

|
The
space available for bearings in a screw compressor is limited by the
close spacing of the rotors. The bearings have to be a type to absorb
radial and axial loading, generally of an angular contact ball bearing
type, which has limited capacity in both directions. This is further
worsened by the high speed that these machines run at to obtain reasonable
efficiency. The effect of bearing failure is often complete destruction
of the compressor.
The vane compressor has no limits on bearing size, and produces radial
loading only. By using parallel roller bearings of sufficient size
it is probable that the majority of vane compressors will use only
one set of bearings throughout their life. |

|
The
auxiliary components of the vane and screw machines are similar. They
both use an oil tank, separator, oil cooler, thermal bypass, minimum
pressure valve, high temperature switch, and some means of controlling
capacity. The maintenance of these items i.e. oil, filter and separator
changes, would be similar. However, if repair is needed on the compressor
alone then the screw compressor is more difficult and costly. In most
cases it is handled on a factory exchange basis. The vane compressor
can be serviced easily in the field. Typically the blades, which are
the only wearing part, can be replaced in one to two hours depending
on size. There are no critical clearances, which have to be measured
and adjusted. |

|
The
failure of an air-end in a screw compressor can cost twenty to forty
percent of the cost of a new unit. A set of blades for a vane compressor
will cost less than ten percent of unit cost new. |

|
When
a screw air-end fails, a wait of several days or weeks is entailed
because these are expensive and not carried by most dealers. Parts
for the vane compressor are less costly and can be carried by dealers. |
|